
A modern and elegant design for professions where corporate image is a crucial pillar for customer service.
FUNCTIONALITYOur shoes are specifically tailored to aviation professionals and address the needs of ergonomics (foot comfort and support), breathability, sweat absorption, thermal insulation, and slip resistance.
COMFORTThe shoes are designed to provide maximum comfort, an essential requirement for professionals who must stand for long hours.
We manufacture in Spain, putting all our effort into achieving the highest quality shoe with leather uppers, antibacterial technical microfiber lining, non-slip sole, and ergonomic lasts to meet the comfort, durability, and elegance requirements of cabin crew and pilots' professions.
EXTERNAL AND INTERNAL MATERIALThe upper part of all Zeddea shoes is made of leather, which helps the shoe adapt to the shape of the foot with use, while facilitating breathability and thermal protection to prevent excessive sweating in warm environments and insulation in cold environments. The leather used in our shoes is national cowhide leather. The lining and insole material is antibacterial technical microfiber, breathable, and absorbent.
The insole is made of a combination of highly resistant materials that provide structural strength to the shoe in the rear, covered with memory-foam foam for greater foot comfort.
LASTThe lasts we use are developed in our own design studio. They then undergo a lengthy process of fitting and comfort testing until their final shape is defined, always prioritizing comfort while not forgetting elegance. Therefore, all the lasts we use at Zeddea to manufacture our shoes, whether rounded toe, square toe, or even pointed toe, allow the toes to fit comfortably inside the shoe and provide enough space to allow the foot to expand throughout the workday.
INSOLEA good insole can considerably improve shoe comfort. We take this into account, so ours are padded with memory-foam polyurethane foam to provide good pressure distribution on the sole of the foot and prevent the appearance of overloaded areas. Additionally, it is breathable to prevent moisture buildup.
OUTSOLEWe use TPU, a highly resistant, flexible, and non-slip material for sole manufacturing. Additionally, it has a footprint pattern that promotes slip-resistant properties.
HEELThe shoe must be stable to prevent falls and twists. Our heels have a wide base, are not too high, and are correctly aligned and balanced with respect to the heel and sole of the shoe, a very important aspect to provide stability and durability. The heel material is a high-resistance polymer (ABS) with shock-absorbing properties, painted with pad printing.
DESIGN AND MANUFACTURING PROCESSAt Zeddea, we are committed to developing quality footwear, which is why we strive every day to ensure that the design and manufacturing processes of our shoes are meticulous and detailed.
The leathers we work with have been carefully chosen and meet the requirements of resistance, flexibility, and safety, meaning they do not contain any chemical substances.
The manufacturing process of Zeddea footwear, although supported by technological tools, is purely artisanal, so the experience and "know-how" of our personnel are crucial to achieving an excellent product. The manufacture of our shoes requires an average of 20 different components and 32 different processes.
We start a new model by first designing the last, a fundamental part that determines the fit and comfort of the shoe. This process is carried out by the model maker together with the last manufacturer. Subsequently, the heel, upper, insole, and sole are designed.
To ensure that all our shoes meet the level of quality, design, and comfort, we proceed to the final quality control. A technical fitting test is carried out, and finally, its comfort is checked with a specific group of users.
Once the model has been approved by our development department, it moves on to the production phase. In this process, the different sizes are scaled, patterns are prepared, and it is delivered to the factory. There, processes such as leather selection, material provisioning, machining, molding, assembly, gluing, finishing, and quality control take place.
The final result is the pair of flight attendant shoes or pilot footwear that our customers receive satisfactorily at their homes, ready to face long workdays without losing their appeal and providing maximum comfort possible.
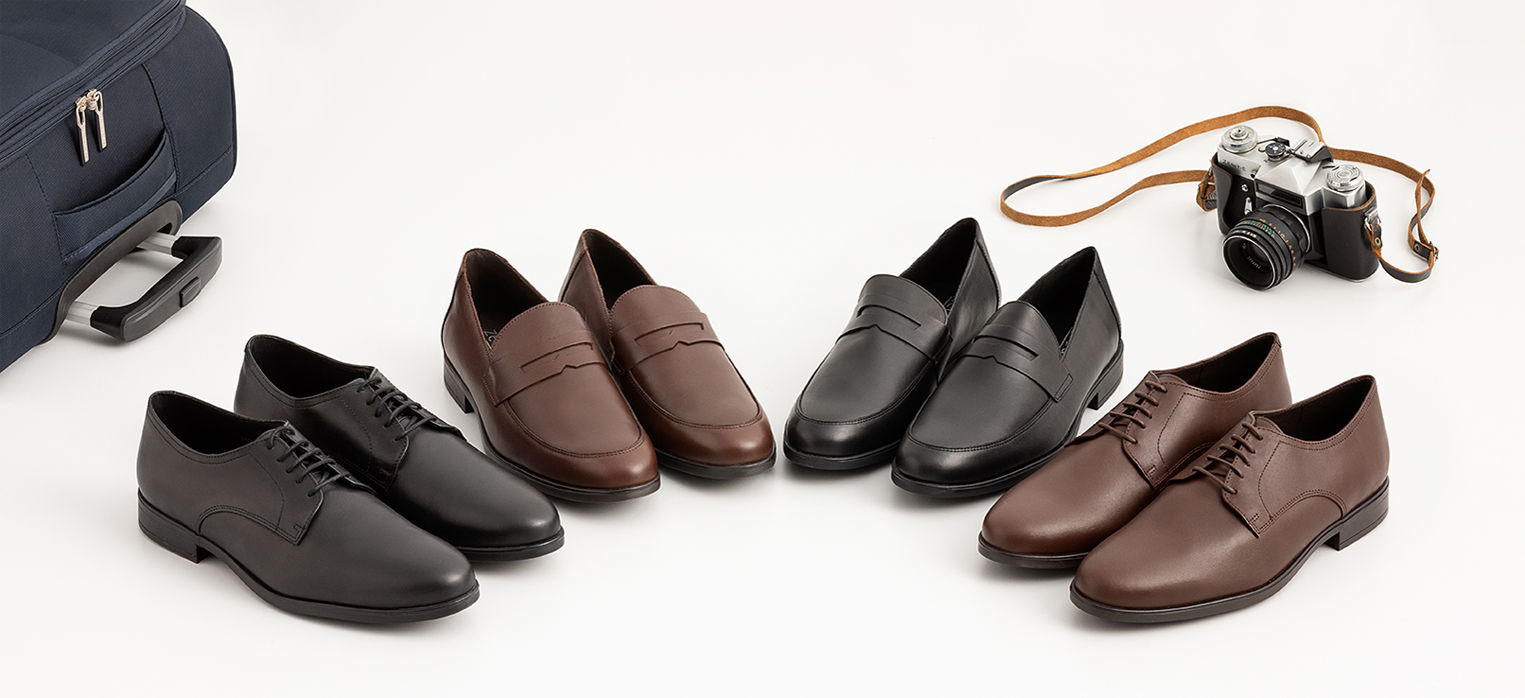